Powernest: 2D true shape nesting library
World’s best true shape nesting library for your software application
Powernest is a powerful and comprehensive library for automatic nesting of complex 2D shapes.
This nesting library has been designed to be integrated into CAM or ERP applications that provide cutting optimization features.
The nesting library adresses a wide range of sectors: sheet metal working, shipbuilding, packaging industry, wood panel or plastic cutting, synthetic or composite materials, etc.
Try our nesting with your parts.
Key benefits
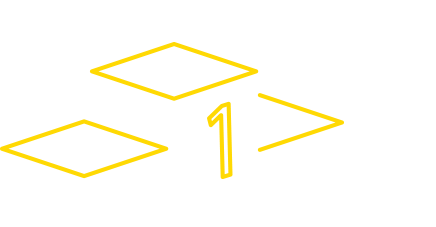
Unparalled nesting performance
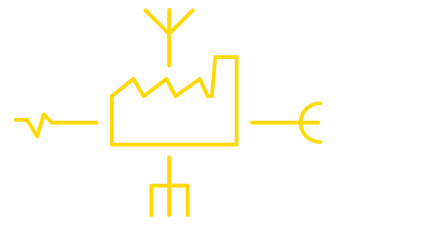
Supports various industry requirements
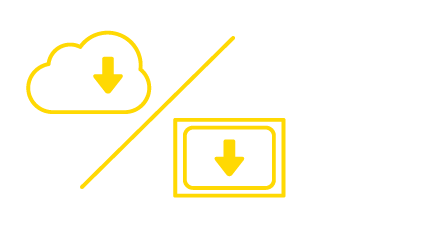
Available as a DLL or in the Cloud
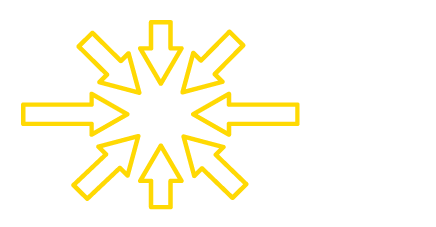
Fast and easy integration
Available as a DLL or in the Cloud as a Web service
Powernest DLL
- C DLL
- No internet connection needed
- Lifetime license
- Maintenance contract included
- 32/64 bits, multithreaded
Powernest WS
- SaaS REST API
- Scalability & 24×7 Availability
- Lower entry cost, SaaS Pricing
- Always up to date
- Unlimited calculation power
Main technical features
Full-featured nesting capabilities for maximum performance
Get the best of true shape nesting
- Best orientation is chosen by the algorithms among allowed orientations
- Parts recesses are used to recursively nest parts into other part
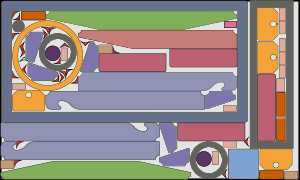
Multi-format
- Global optimization on multiple sheets to save more material
- Sheets of different sizes and offcuts may be reused
- Improve productivity by using the same layout several times (multiplicity)
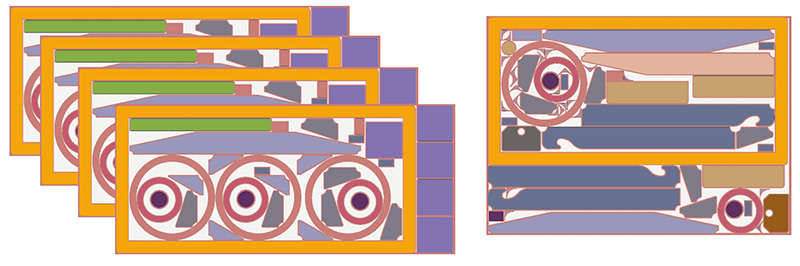
Arbitrary non-rectangular formats
- Nests parts into non-rectangular sheets
- Allow reuse of offcuts
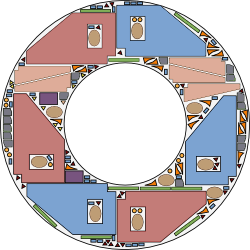
Run full automatic or improve nesting interactively
Full automatic nesting
- No human intervention needed, runs as “black box”
- Simple to use: allow more time to get better performances
Manual nesting capacity
- Start nesting manually and continue in automatic mode
- Optimize the use of remaining free surface without modifying the position of part already nested
- Improve automatic nesting by positioning specific parts manually
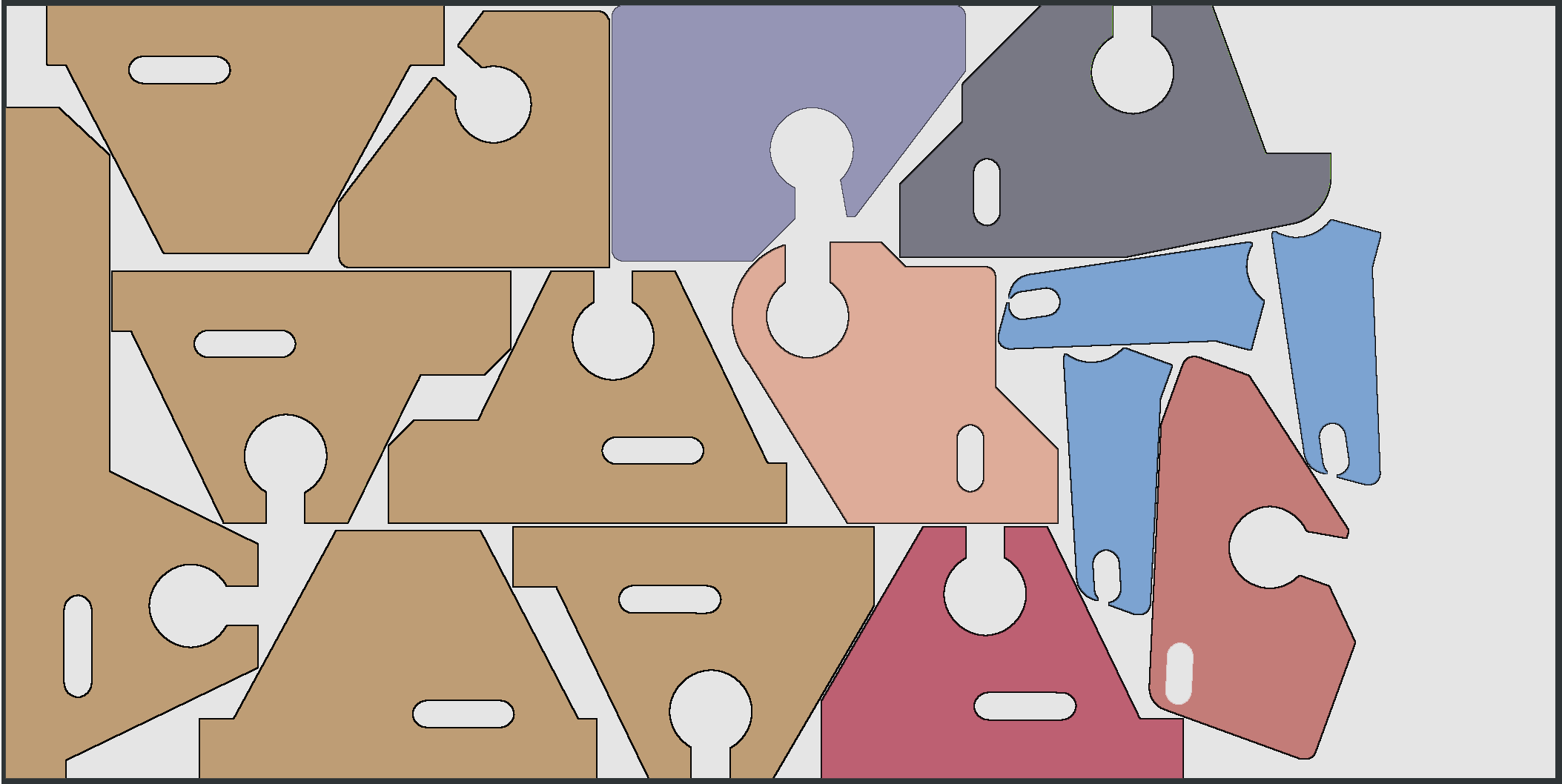
Domain constraints for better quality
Production-ready nesting taking into account all your constraints
- Taking into account the patterns on material formats and parts to be placed: lines, squares, grid, etc.
- Nesting with priority groups
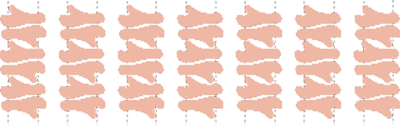
Define a custom security area around parts
- Custom security areas improve performance much more than using global offsets values
- Security areas may overlap for better performance
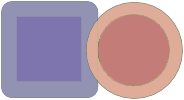
Defect and quality zone management
- Define zones where parts can or cannot be nested
- Perfectly suited for heterogeneous materials
- True-shape defect definition for better performance
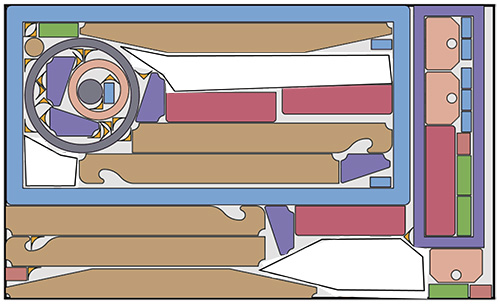
Common cutting
- Nest parts sharing one segment just at tool distance, so that they can be cut in a single pass
- Reduce cutting cycle time
- Save material
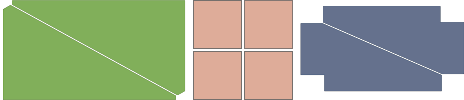